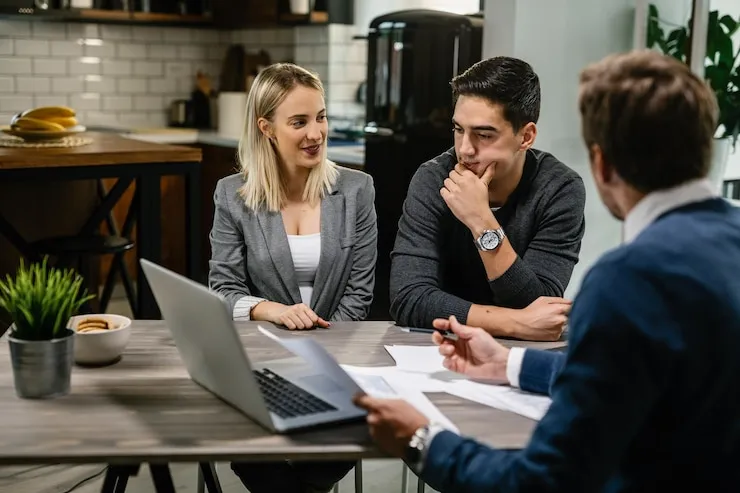
At Pearl Lemon Consulting, we’ve seen firsthand how operational inefficiencies, slow workflows, and wasteful processes hold businesses back. That’s why we work directly with organizations like yours to implement Lean Management Consulting strategies that deliver real results. From reducing waste to improving workflows with proven methodologies like Value Stream Mapping, Just-In-Time production, and Kaizen principles, we help businesses operate smarter and achieve measurable outcomes.
We don’t offer generic advice. Everything we do is grounded in fact based methodologies and designed to your industry’s challenges. Businesses we’ve worked with have reported up to 30% cost savings, 20% productivity gains, and significantly better quality metrics.
Our Core Lean Management Services
When we work with you, we bring the full range of Lean Management tools to the table. From process mapping to leadership development, we ensure every layer of your organization is improved for efficiency.


Process Streamlining
Let’s address inefficiencies head on. By using tools like 5 Whys and Ishikawa Diagrams, we’ll uncover the root causes of your operational bottlenecks. From there, we’ll redesign your processes to eliminate waste and streamline workflows.
For instance, when we worked with a logistics company, our introduction of Kanban scheduling improved warehouse efficiency, cutting delivery delays by 30%.

Lean Digital Upgradation
Digital tools are an essential part of today’s Lean practices. We’ll integrate IoT devices, real-time analytics dashboards, and predictive maintenance tools into your existing systems to improve oversight and reduce downtime.
A recent client in the automotive sector saw 20% maintenance cost reductions by shifting from reactive to predictive maintenance using sensor data.

Leadership and Team Training
Lean isn’t just about processes; it’s about people. We’ll work with your leadership team to conduct Gemba Walks, lead Kaizen events, and use Visual Management tools to align your team.
One healthcare client reduced patient wait times by 40% by better-balancing workloads with Takt Time analysis and strategic staffing adjustments.
Industry Specific Lean Solutions
We understand that each industry operates differently. That’s why we bring specific expertise to sectors like manufacturing, retail, healthcare, and logistics, delivering solutions that align with your business model.
Manufacturing
- Challenge: Unscheduled downtime due to poor equipment utilization.
- Our Approach: Introducing Heijunka (level production) and improving maintenance schedules.
- Results: A mid sized production firm saw a 15% increase in efficiency while maintaining consistent quality standards.
Retail
- Challenge: Overstocking and markdowns due to inaccurate demand forecasting.
- Our Approach: Implementing Just In Time inventory systems and fine tuning replenishment models.
- Results: One retailer saved £100,000 annually through reduced stockouts and excess inventory.
Healthcare
- Challenge: Patient throughput delays in outpatient clinics.
- Our Approach: Using Value Stream Mapping to identify bottlenecks and reallocate staff.
- Results: A leading healthcare provider cut patient wait times by 50%, improving overall satisfaction scores.
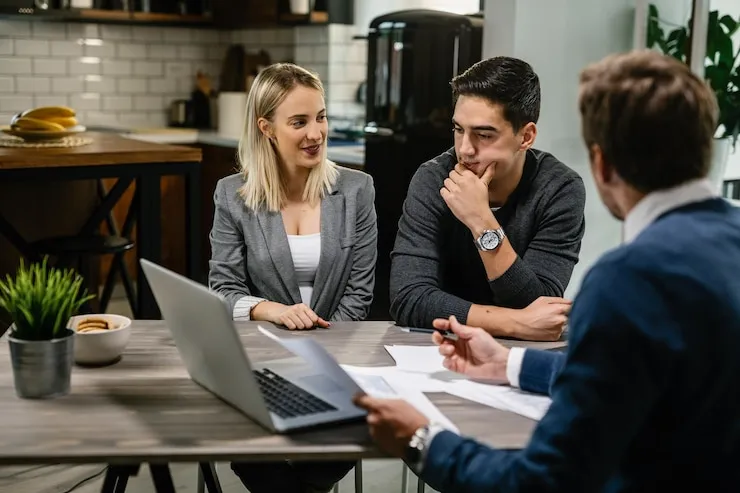
Why Work with Us?
When you partner with Pearl Lemon Consulting, you’re not just hiring a consultancy you’re gaining a team that understands the complexities of your industry. We know that businesses face mounting challenges like rising costs, evolving customer expectations, and the need for greater efficiency. Our approach focuses on actionable strategies, measurable results, and long-term improvements that directly impact your bottom line.
We’ve worked with organizations across sectors, from manufacturing plants struggling with high defect rates to healthcare providers overwhelmed by patient backlogs. Our experience means we bring solutions that work in real world settings, not just in theory.
- We Build Systems for the Future
Our solutions aren’t quick fixes they’re built to last. By combining traditional Lean tools with real-time monitoring technologies, we ensure continuous improvement becomes part of your business DNA
- We Speak Your Language
With years of experience in industries like manufacturing, logistics, and healthcare, we understand the challenges you face. From tracking COPQ (Cost of Poor Quality) to implementing Poka-Yoke (error-proofing), we use solutions that make sense for your business.
- We Deliver Results You Can See
We measure success by the numbers. Whether it’s cutting lead times by 25%, improving first-pass quality rates, or achieving significant cost savings, our focus is on tangible outcomes for your business.
How We Work with You
Our process is designed for clarity, collaboration, and measurable results. Here’s how we work with you:
Assessment
We analyze your operations by conducting Gemba Walks, and observing processes in action to identify inefficiencies, bottlenecks, and opportunities for improvement.
Planning
Using insights from the assessment, we create a Lean roadmap that may involve implementing 5S, improving workflows, or aligning production with Takt Time for better balance.
Execution
We collaborate closely with your team to implement solutions such as Kanban systems, process automation through IoT tools, and Lean strategies that deliver immediate impact.
Sustainability
To ensure long term success, we establish KPIs like OEE and train your team to monitor, adjust, and maintain the improvements independently.
Frequently Asked Questions
Lean focuses on eliminating waste, while Six Sigma targets defect reduction through statistical analysis. Together, they create a powerful approach to process improvement.
Most of our clients see measurable improvements—like reduced lead times and cost savings—within 3-6 months of implementation.
Absolutely. Lean principles are scalable and can make a big difference, especially for businesses with limited resources.
Depending on your needs, we may use tools like Kanban systems, Takt Time analysis, Poka-Yoke, and Jidoka (autonomation), along with advanced digital solutions like predictive analytics.
Ready to Solve Your Operational Challenges?
At Pearl Lemon Consulting, we’re committed to helping you eliminate waste, improve workflows, and achieve measurable results. If inefficiencies are holding you back, let’s fix them. Schedule a free consultation today, and let’s build smarter, more efficient operations together.